Understanding Injection Molding Plastic: The Ultimate Guide
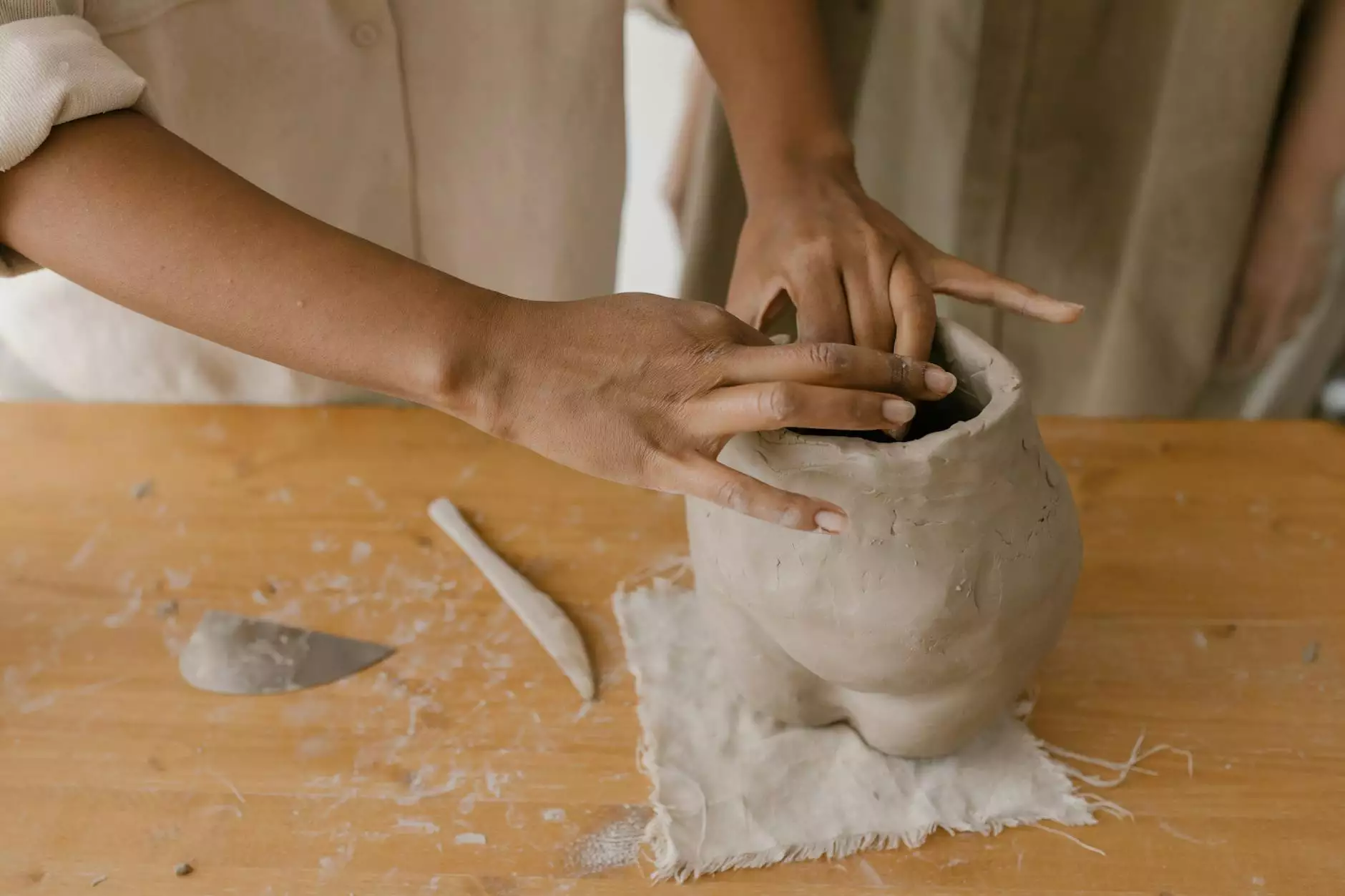
Injection molding plastic is a revolutionary manufacturing technique that has transformed various industries by enabling the mass production of complex parts. In this comprehensive guide, we will explore every aspect of injection molding, from its process and materials to its applications across different sectors. Our goal is to provide you with valuable insights that will help your business harness the full potential of injection molding plastic.
What is Injection Molding Plastic?
Injection molding is a manufacturing process used to produce parts by injecting molten material into a mold. This method is particularly popular in the production of plastic parts due to its efficiency and precision. The molds used in this process are made from durable materials, enabling the production of high-quality components that meet stringent industry standards.
How Injection Molding Works
The process of injection molding can be broken down into several key steps:
- Material Selection: Various types of plastics, including thermoplastics and thermosetting polymers, can be used based on the specific requirements of the product.
- Melting: The selected plastic pellets are heated until they reach a molten state.
- Injection: The molten plastic is injected into the mold cavity under high pressure, ensuring even distribution.
- Cooling: The plastic cools and solidifies within the mold, taking the shape of the desired part.
- Ejection: Once cooled, the mold opens, and the finished part is ejected.
Materials Used in Injection Molding
One of the significant advantages of injection molding plastic is the variety of materials that can be employed. Some common materials include:
- Polypropylene: Known for its lightweight and flexibility, making it ideal for a wide range of applications.
- Polyethylene: Highly resistant to impact and moisture, suitable for various consumer products.
- ABS (Acrylonitrile Butadiene Styrene): Offers a good balance of strength and ductility, frequently used in consumer electronics.
- Polycarbonate: Renowned for its toughness and clarity, often utilized in safety glasses and automotive components.
- Nylon: Excellent resistance to wear and chemicals, commonly used in mechanical parts.
Benefits of Injection Molding Plastic
Investing in injection molding plastic can yield a plethora of benefits for businesses:
- Cost-Effective: Once the mold is created, producing each part becomes cheaper, especially for large volumes.
- High Precision: Molds can produce parts with very tight tolerances, ensuring consistency in dimensions.
- Rapid Production: This method allows for the quick production of large quantities, serving high-demand markets efficiently.
- Complex Geometries: Injection molding can create complex designs that would be challenging with other manufacturing methods.
- Reduced Waste: The process minimizes material waste, as excess plastic can often be recycled back into the system.
Applications of Injection Molding Plastic
Injection molding is utilized across numerous sectors, showcasing its versatility:
1. Automotive Industry
Injection molding plays a pivotal role in the automotive industry by enabling the manufacture of components such as:
- Dashboard panels
- Interior trim
- Headlight housings
- Various clips and fasteners
2. Consumer Electronics
It is also a critical method in producing parts for consumer electronics like:
- Smartphone casings
- Remote controls
- Housings for computers and laptops
- Wearable technology casings
3. Medical Devices
In the medical field, injection molding is vital for creating:
- IV bags
- Surgical instruments
- Medical packaging
- Prosthetics
4. Toys and Sporting Goods
Injection molding is extensively used for:
- Action figures
- Board game pieces
- Sporting equipment
Choosing the Right Injection Molding Service Provider
Partnering with the right injection molding service provider can significantly impact your production efficiency and product quality. Here are key factors to consider when selecting a partner:
- Experience: Look for a provider with a solid track record in the industry.
- Capabilities: Ensure they have the necessary machinery and technology for your project.
- Quality Assurance: Choose a partner that adheres to strict quality control measures and certifications.
- Customer Service: Opt for a company that values communication and support throughout the process.
- Cost-Effectiveness: Evaluate their pricing structure to find a balance between quality and affordability.
Conclusion: The Future of Injection Molding Plastic
As industries continue to evolve, injection molding plastic will remain at the forefront of manufacturing innovation. Its ability to produce complex, high-quality parts quickly and cost-effectively makes it an indispensable method for businesses across various sectors. By understanding the intricacies of this process, companies like DeepMould.net can strategically utilize injection molding to enhance their product offerings and stay competitive in the global marketplace.
Investing in the latest technologies and sustainable practices will further propel the growth of injection molding, allowing manufacturers to meet the increasing expectations for efficiency and environmental responsibility. Embrace the potential of injection molding plastic, and watch your business thrive in this ever-evolving landscape.