The Future of Manufacturing: Understanding 3D Prototyping in Metal Fabrication
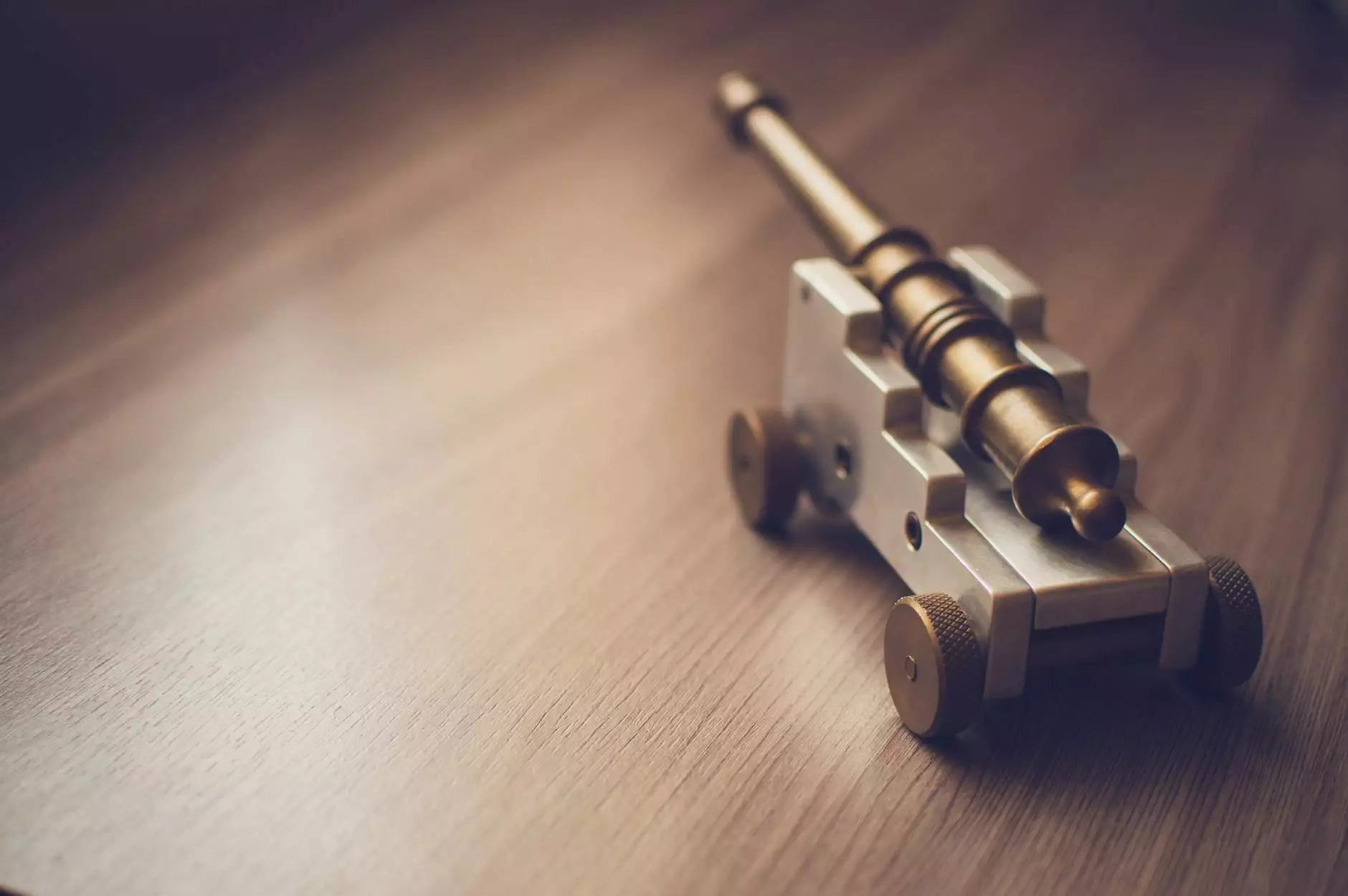
In today’s fast-paced industrial landscape, the ability to innovate quickly and effectively is crucial for success. One of the most transformative technologies reshaping this landscape is 3D prototyping. This article delves into the ins and outs of 3D prototyping within the metal fabrication sector, illustrating how it serves as a catalyst for improvement and innovation, particularly for businesses like DeepMould.net.
What is 3D Prototyping?
3D prototyping refers to the process of creating a three-dimensional model of a physical object using computer-aided design (CAD) software. This model is then used to create a prototype through various methods, most commonly additive manufacturing (3D printing). The primary goal of 3D prototyping is to visualize and test a design before mass production.
The Importance of 3D Prototyping in Metal Fabrication
Metal fabricators have much to gain from integrating 3D prototyping into their workflow. The importance arises from several key factors:
- Rapid Prototyping: Traditional methods of prototyping can take a significant amount of time. 3D prototyping can significantly reduce this timeline, enabling businesses to produce prototypes in days rather than weeks.
- Cost Efficiency: By using 3D prototyping, companies can minimize waste and reduce material costs, ensuring that budget allocation is optimized.
- Design Flexibility: The technology allows for complex designs that are often unachievable with traditional machining methods.
- Testing and Validation: Prototypes can be tested and iterated upon before full-scale production, which reduces the risk of design flaws.
How 3D Prototyping Works
The 3D prototyping process involves several key steps:
1. Conceptualization
Every 3D prototyping project begins with a concept. Designers come up with ideas which are often drawn from sketches or CAD models that define the object’s parameters and functionalities.
2. Computer-Aided Design (CAD)
Designers use CAD software to create detailed models of the prototype, ensuring precision and adherence to specifications.
3. 3D Printing
Once finalized, the digital model is sent to a 3D printer. Various materials can be used depending on the intended use, including plastics, resins, and metals.
4. Post-Processing
After printing, the prototype undergoes post-processing, which may include cleaning up the model, smoothing surfaces, and applying finishes.
5. Testing and Iteration
Once the prototype is ready, it is tested rigorously. Feedback gained from testing leads to revisions in the design, which can be quickly implemented thanks to the rapid nature of 3D prototyping.
Case Study: How DeepMould.net Utilizes 3D Prototyping
DeepMould.net, as a leading provider of metal fabrication solutions, has strategically incorporated 3D prototyping into its processes. Here are some examples of how the company utilizes this technology:
Streamlining Design Processes
By integrating 3D prototyping, DeepMould.net has been able to enhance the design phase of its projects. Quick iterations enable the design team to explore multiple concepts and arrive at an optimal solution faster.
Enhancing Product Quality
With the ability to prototype quickly, DeepMould.net can conduct extensive testing on new designs. This focus on quality ensures that the final product exceeds customer expectations.
Improving Customer Collaboration
3D prototyping allows DeepMould.net to present tangible prototypes to clients, facilitating better communication and collaboration. Clients can visualize the end product, leading to enhanced satisfaction.
Advantages of 3D Prototyping Over Traditional Prototyping Methods
While traditional prototyping methods have served the industry well, 3D prototyping offers several advantages:
- Speed:3D prototyping reduces the time from concept to prototype, enabling quicker product launches.
- Affordability: The reduction of waste and the ability to use less expensive materials lowers overall costs.
- Complexity: The intricate designs that can be achieved through 3D prototyping often cannot be realized through traditional methods.
- Customization: It allows for easy alterations and customization, making it ideal for bespoke products.
The Future of 3D Prototyping in Metal Fabrication
The future of 3D prototyping in metal fabrication looks incredibly promising. As technology continues to advance, we can expect the following trends to emerge:
1. Increased Use of Advanced Materials
As new materials are developed, 3D prototyping will leverage these innovations, providing stronger and lighter prototypes with enhanced properties.
2. Integration with AI and Machine Learning
Artificial intelligence could aid in design optimization by assessing performance metrics and suggesting improvements to current designs, streamlining the prototyping process even further.
3. Greater Accessibility
As 3D printing technology becomes more affordable, smaller businesses will gain access to prototyping, leveling the playing field across the industry.
Conclusion
In summary, 3D prototyping is revolutionizing the field of metal fabrication. Companies like DeepMould.net are at the forefront of this evolution, utilizing the technology to enhance their workflows, improve product quality, and foster better customer relationships. As the industry continues to embrace this technology, we can anticipate significant advancements in manufacturing processes, ensuring that businesses stay competitive in a rapidly changing world. The future of manufacturing is here, and it relies on the powerful capabilities of 3D prototyping.
3 d prototyping