The Future of Precision Injection Mould in Metal Fabrication
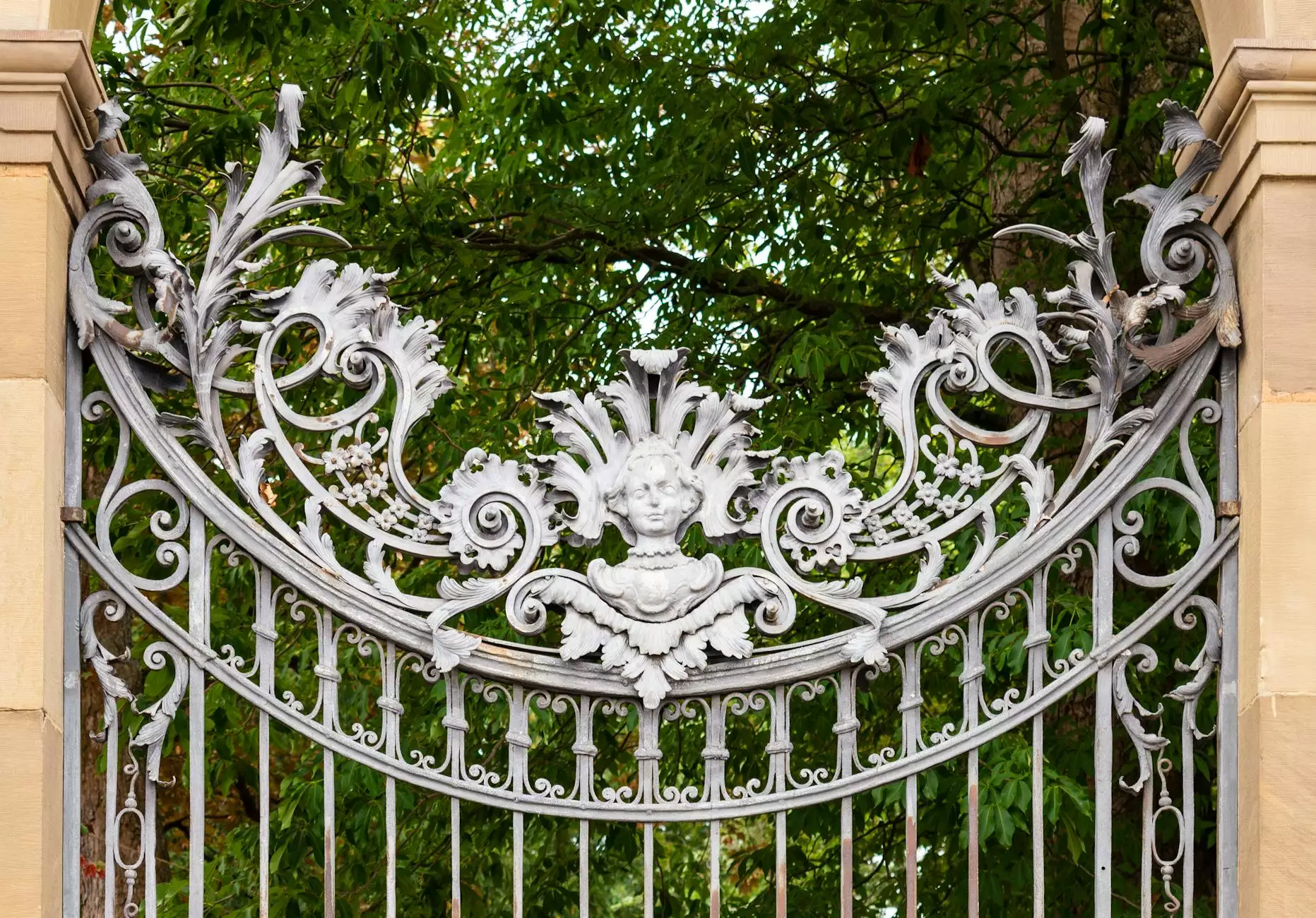
In the dynamic world of metal fabrication, the role of precision injection mould technology cannot be overstated. As businesses strive for excellence and efficiency, the demand for high-quality metal parts has surged. This article delves into the intricacies of precision injection mould and its transformative impact on the metal fabrication industry.
Understanding Precision Injection Moulding
Precision injection moulding is a manufacturing process that involves injecting molten material into a pre-prepared mould cavity to create components with intricate shapes and forms. This technique is particularly advantageous in the production of parts that require high precision and consistency. The process is widely used not only for plastic parts but also increasingly for metal components, where accuracy and repeatability are essential.
Key Benefits of Precision Injection Moulding
- High Precision: Achieving tight tolerances for intricate designs, essential for structural integrity and performance.
- Consistency: Mass production of identical parts ensures uniform quality across batches.
- Efficiency: Reduced cycle times lead to increased productivity, enabling manufacturers to meet market demands swiftly.
- Complex Geometries: The ability to produce complex shapes that would be difficult or impossible to achieve through traditional machining methods.
- Material Versatility: Compatible with a range of materials, including various metals, composites, and plastics.
The Role of Metal Fabricators in Utilizing Precision Injection Mould
Metal fabricators are pivotal in harnessing the power of precision injection mould technology. By integrating this advanced technique into their operations, they can enhance their capabilities, offering clients high-quality products that meet rigorous standards. Here’s how metal fabricators can leverage this technology:
1. Streamlining Production Processes
By adopting precision injection mould, metal fabricators can significantly streamline their production processes. Automation of the injection process minimizes human error and allows for faster manufacturing cycles. This streamlining not only reduces operational costs but also enables businesses to respond to customer demands more effectively.
2. Enhancing Design Flexibility
Modern clients often require customized solutions. With the capabilities of precision injection moulding, fabricators can create bespoke designs without compromising on quality or efficiency. This flexibility attracts a broader customer base, as businesses can cater to niche markets with specialized needs.
3. Ensuring Quality Control
Quality assurance is a critical aspect of manufacturing. Precision injection mould allows for extensive quality control measures throughout the production process. From initial design validation through to final product inspection, fabricators can ensure that every part meets the exact standards required in today's competitive environment.
Industry Applications of Precision Injection Moulding
The versatility of precision injection mould makes it suitable for a vast array of industries. Here are some of the key sectors benefiting from this technology:
Aerospace
The aerospace industry demands components that are both lightweight and durable. Precision injection moulding provides the ability to produce intricate parts that meet stringent safety and performance criteria, fostering innovation in aircraft design.
Automotive
The automotive sector utilizes precision injection mould to manufacture everything from engine components to interior fittings. The efficiency of this process allows car manufacturers to produce high volumes of parts while maintaining the quality necessary for safety and reliability.
Electronics
In the electronics industry, precision is critical. Injection moulding enables the production of complex circuitry and detailed housing components that not only function effectively but also enhance the aesthetic appeal of electronic devices.
Medical Devices
The production of medical devices requires the utmost precision and reliability. With precision injection mould, manufacturers can create parts that meet rigorous standards, ensuring safety and efficacy in critical applications.
Challenges and Solutions in Precision Injection Moulding
Despite its advantages, precision injection mould is not without challenges. Key issues may include material selection, mould design, and production costs. However, there are effective solutions to these challenges, enabling businesses to thrive:
Material Selection
Choosing the right material is vital for successful moulding. Manufacturers should engage in thorough research and testing to identify materials that provide the best properties for their specific applications.
Mould Design
Investing in advanced CAD (Computer-Aided Design) software can significantly improve mould design, allowing for more complex geometries and better heat dispersion.
Cost Management
Undertaking comprehensive cost analysis and efficiency assessments can help businesses manage the high initial costs associated with precision injection mould. Streamlined operations and increased production rates often lead to long-term savings.
Future Trends in Precision Injection Moulding
The future of precision injection mould in metal fabrication looks promising, with several trends emerging:
1. Integration of Automation and AI
The integration of automation and artificial intelligence (AI) into the injection moulding process is set to revolutionize production capabilities. AI can optimize production schedules, predict potential maintenance issues, and enhance quality control efforts.
2. Sustainability Focus
As the world steers towards more sustainable practices, precision injection moulding is also evolving. Innovations in biodegradable materials and energy-efficient processes are becoming increasingly important for manufacturers looking to reduce their environmental footprint.
3. Advanced Materials Development
Research and development in new materials will continue to propel the industry forward. With the introduction of composites and advanced alloys, manufacturers will enjoy enhanced properties such as durability, weight reduction, and thermal stability.
Conclusion
As the metal fabrication industry continues to evolve, the importance of precision injection mould technology will only increase. Businesses that invest in this advanced manufacturing technique position themselves at the forefront of innovation, preparing to meet the challenges of tomorrow with agility and precision. By focusing on quality, efficiency, and sustainability, metal fabricators can thrive in an ever-competitive marketplace.
The potential of precision injection mould is vast, and as technology advances and industry standards rise, it remains a critical area for continued investment and exploration. Those who embrace this technology will not only enhance their manufacturing capabilities but will also contribute to a future defined by innovation and excellence.