High Pressure Die Casting Machine: Revolutionizing Metal Fabrication
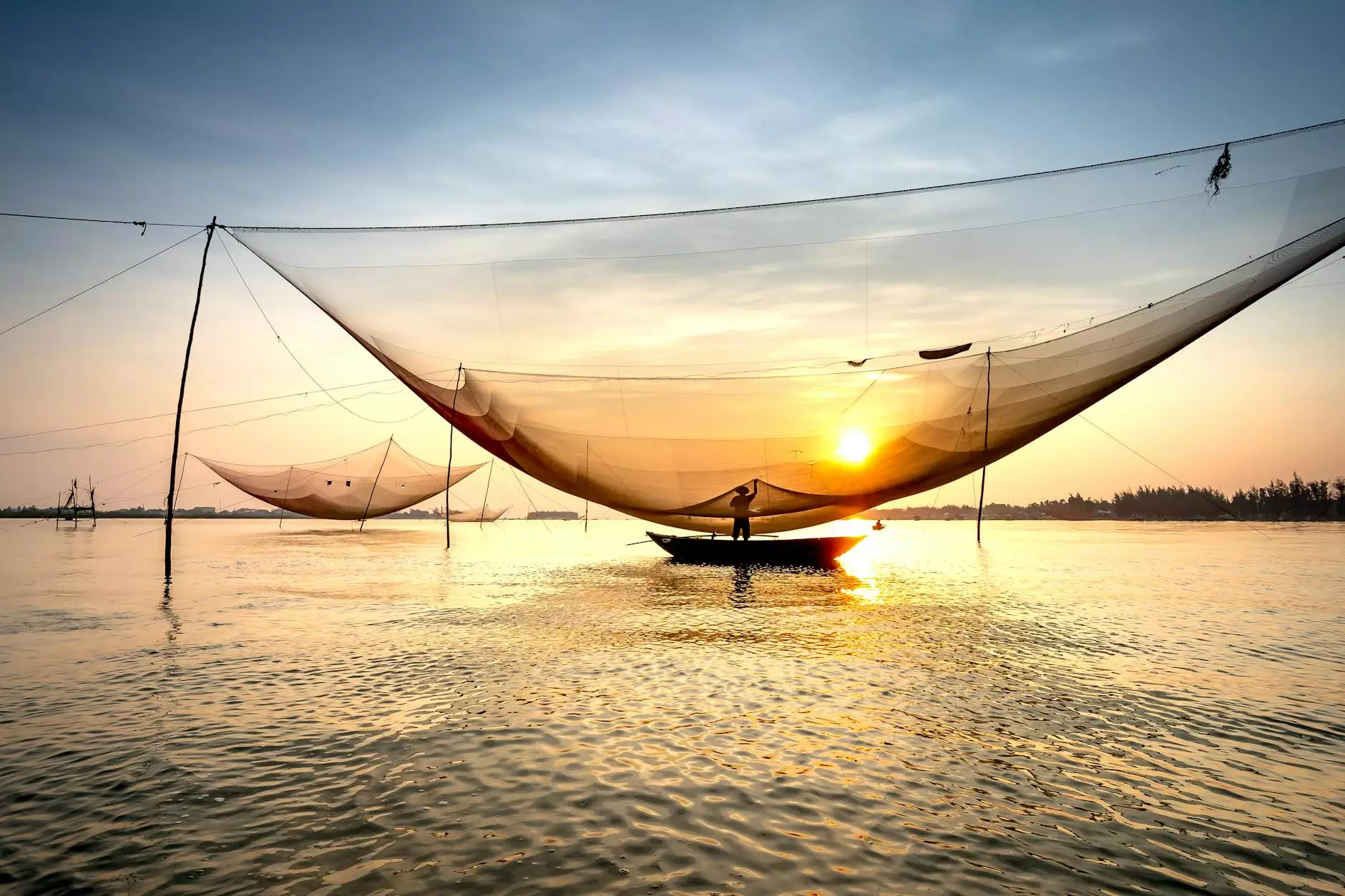
In the modern era of manufacturing, precision and efficiency are paramount. One of the technological marvels that have greatly contributed to achieving these goals in the metal fabricators sector is the high pressure die casting machine. This article delves deep into the intricacies of high pressure die casting, exploring its mechanisms, advantages, applications, and the future it promises for the manufacturing industry.
Understanding High Pressure Die Casting
The high pressure die casting machine operates by forcing molten metal into a reusable mold at high pressure. This process allows for the production of parts with excellent dimensional accuracy and surface finish. The transformation begins when metal is melted and poured into the machine's die, where it solidifies under pressure, ensuring that every detail of the mold is captured.
The Mechanics Behind the Process
To comprehend how a high pressure die casting machine works, it is essential to break down its operations:
- Melting: The metal is heated until it reaches a molten state in a melting furnace.
- Injection: A plunger or piston injects the molten metal into the mold at extremely high speeds.
- Cooling: The metal is allowed to cool and solidify under pressure, which prevents gas entrapment.
- Ejection: Once solidified, the die opens, and the cast part is ejected.
Types of Metals Used in High Pressure Die Casting
The versatility of the high pressure die casting machine extends to the variety of metals that can be used in the process:
- Aluminum: Known for its light weight and resistance to corrosion, aluminum is commonly used for various applications.
- Zinc: It is particularly advantageous for its low melting point and excellent fluidity, making it ideal for complex shapes.
- Magnesium: This metal is appreciated for its strength-to-weight ratio, making it suitable for automotive and aerospace components.
- Copper: Often employed for electrical materials due to its high conductivity.
Benefits of High Pressure Die Casting
The implications of utilizing a high pressure die casting machine are vast, affecting both production processes and the final outcomes of products. Here are some notable benefits:
1. Exceptional Dimensional Accuracy
One of the primary advantages of high pressure die casting is its capability to produce parts with high dimensional accuracy. The precision of this manufacturing method is critical in industries where tolerances are stringent.
2. High Production Efficiency
With the ability to produce large quantities of parts quickly, the high pressure die casting machine significantly enhances productivity. The cycle time is short, typically ranging from 30 seconds to a few minutes, depending on the part's complexity.
3. Superior Surface Finish
Parts produced through high pressure die casting often require minimal machining due to their superior surface finish, allowing for reduced handling and processing costs.
4. Material Savings
The process is highly efficient in material use, as the die casting method significantly reduces waste compared to traditional manufacturing techniques.
Applications of High Pressure Die Casting
The versatility of the high pressure die casting machine makes it suitable for a wide array of applications across various industries:
Automotive Industry
In the automotive sector, die casting is used to manufacture a variety of components such as:
- Engine blocks
- Transmission housings
- Structural parts
Electronics Industry
High pressure die casting plays a crucial role in the production of intricate components that require excellent conductivity, including:
- Connectors
- Heat sinks
- Casings
Aerospace Industry
Parts that demand high strength-to-weight ratios and precision are commonly manufactured through die casting. Examples include:
- Brackets
- Machinery components
- Housing for electronic systems
The Future of High Pressure Die Casting
As industries evolve, so does technology. The high pressure die casting machine is undergoing significant advancements. Key developments include:
1. Automation and Smart Manufacturing
Integration with automation and IoT technologies is set to enhance the precision and efficiency of die casting processes. Smart machines will monitor operations in real-time, predicting issues before they arise.
2. Sustainable Practices
Given the global push for sustainability, modern die casting manufacturers are exploring lighter metals and innovative recycling methods in their processes. The industry is evolving to embrace more eco-friendly practices.
3. Increased Use of Additive Manufacturing
Combining additive manufacturing with die casting is paving the way for creating intricate designs that were previously unattainable, leading to the development of bespoke solutions for diverse needs.
Conclusion: Embracing the Future of Metal Fabrication
In conclusion, the high pressure die casting machine has established itself as an invaluable asset in the realm of metal fabricators. Its efficiency, accuracy, and versatility make it a cornerstone of modern manufacturing. As technology progresses, the continued evolution of this process promises to unlock new possibilities, driving innovation and sustainability within the industry. Companies like deepmould.net are at the forefront of this movement, committed to advancing the capabilities of die casting to meet the growing demands of the market.